Mini turbo jet fans require strict adherence to safety protocols and regulatory compliance to ensure safe operation across various applications. Safety Standards and Certifications for Mini Turbo Jet Fans encompass multiple international frameworks including CE marking, UL certification, and ISO standards that manufacturers must meet before bringing products to market. These certifications protect both users and manufacturers from potential hazards associated with high-speed rotating equipment.
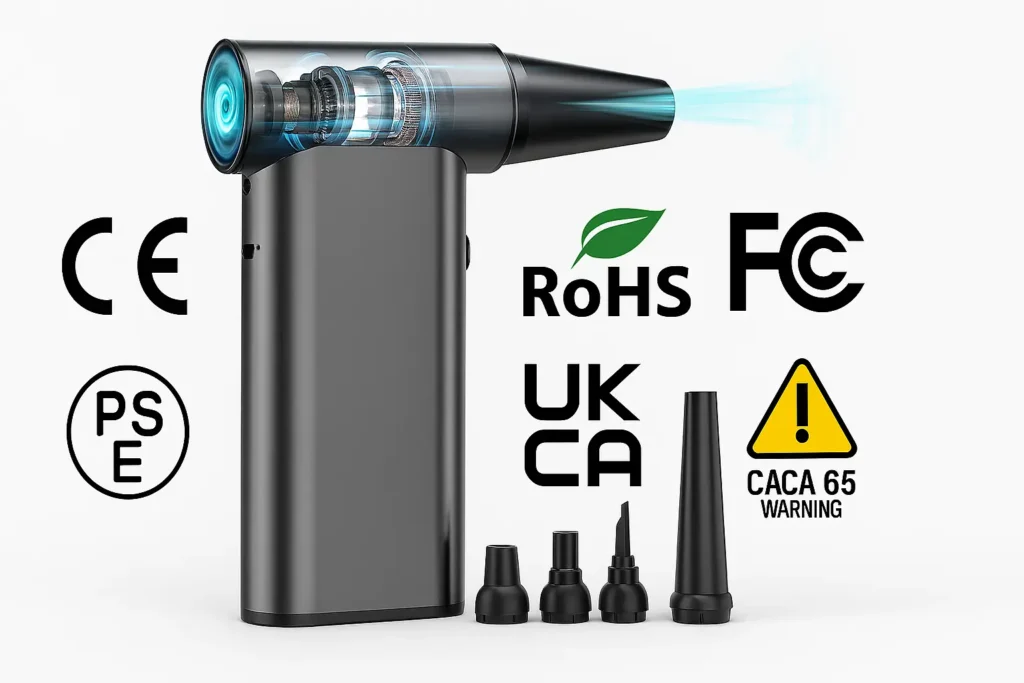
The certification process involves comprehensive testing procedures that evaluate electrical safety, mechanical integrity, and performance under various operating conditions. Manufacturers must implement quality management systems and undergo regular audits to maintain their certification status. Understanding these requirements helps buyers identify legitimate, tested products from reputable suppliers.
Buyers and suppliers benefit from knowing how to verify certification marks and navigate the complex landscape of safety requirements. This knowledge becomes essential when selecting mini turbo jet fans for industrial applications, consumer electronics cooling, or specialized equipment where safety cannot be compromised.
Why Safety And Certification Matter
Proper safety standards and certifications protect users from electrical hazards, mechanical failures, and environmental risks while enabling manufacturers to access global markets. These requirements ensure mini turbo jet fans meet regulatory expectations and build consumer confidence through verified performance standards.
Reducing Risk Of Electrical Or Mechanical Failure
Safety certifications identify potential failure points before products reach consumers. Mini turbo jet fans require IP ratings to protect against moisture and dust ingress, preventing electrical shorts and component damage.
Manufacturers must implement thermal management systems to prevent overheating during extended operation. These systems include temperature sensors, automatic shutoffs, and heat dissipation materials that maintain safe operating temperatures.
ISO 12100 provides machinery safety guidelines that apply to mini turbo jet fans. This standard requires risk assessment documentation, protective measures, and user information to minimize mechanical hazards.
Electrical components need proper insulation and grounding to prevent shock hazards. Certified products undergo rigorous testing for voltage tolerance, current leakage, and insulation resistance under various environmental conditions.
Building Trust In Global Markets
International certifications enable manufacturers to sell products across multiple regions without additional testing. CE marking allows European market access, while UL certification opens North American markets.
Product compliance with recognized standards reduces liability risks for manufacturers and retailers. Certified products demonstrate adherence to established safety protocols and quality control measures.
Export markets often require specific certifications before allowing product imports. These requirements protect local consumers and ensure products meet national safety expectations.
Certification marks on products provide immediate recognition of quality and safety standards. Consumers associate these marks with reliable performance and reduced risk of product failure.
Meeting Buyer And Regulatory Expectations
Regulatory requirements vary by application and installation location. Industrial facilities may require explosion-proof equipment design for hazardous environments, while residential applications focus on noise control and energy efficiency.
Government agencies mandate specific certifications for equipment used in public buildings, healthcare facilities, and educational institutions. These requirements ensure products meet enhanced safety standards for vulnerable populations.
Commercial buyers often specify certified products in procurement contracts. This requirement protects organizations from liability while ensuring equipment reliability and performance consistency.
Environmental impact and sustainability certifications address growing concerns about product lifecycle effects. These standards cover energy efficiency, material sourcing, and end-of-life disposal requirements that buyers increasingly demand.
Overview Of Key Safety Standards
Mini turbo jet fans must comply with region-specific safety standards that regulate electrical safety, electromagnetic compatibility, and hazardous substance restrictions. These certifications ensure consumer protection and market access across different jurisdictions.
CE Marking (Europe)
CE marking indicates conformity with European Union safety, health, and environmental protection standards. Mini turbo jet fans require CE certification to legally enter the European market.
The marking demonstrates compliance with the Low Voltage Directive for electrical safety. It also covers electromagnetic compatibility requirements under the EMC Directive.
Manufacturers must conduct conformity assessments and maintain technical documentation. The CE marking must be visibly affixed to the product or packaging.
Key Requirements:
- Electrical safety testing per IEC 60335 appliance safety standards
- EMC compliance testing
- Technical file documentation
- Declaration of conformity
RoHS Directive (Europe)
RoHS (Restriction of Hazardous Substances) limits dangerous materials in electrical equipment. Mini turbo jet fans sold in Europe must comply with RoHS restrictions on lead, mercury, cadmium, and other substances.
The directive restricts ten hazardous substances to specific concentration levels. Manufacturers must verify supplier compliance throughout the supply chain.
CE RoHS certification requires material testing and supply chain documentation. Non-compliance results in market access restrictions and potential recalls.
Restricted Substances Include:
- Lead (Pb)
- Mercury (Hg)
- Cadmium (Cd)
- Hexavalent chromium (Cr6+)
- Polybrominated biphenyls (PBB)
- Polybrominated diphenyl ethers (PBDE)
FCC Certification (USA)
FCC (Federal Communications Commission) certification ensures mini turbo jet fans meet electromagnetic interference standards. Electronic devices must not cause harmful interference to radio communications.
FCC EMC compliance requires testing at accredited laboratories. Manufacturers must obtain equipment authorization before marketing products in the United States.
The certification process involves emissions testing and susceptibility evaluation. Products must display FCC identification numbers and compliance statements.
Testing Requirements:
- Conducted emissions testing
- Radiated emissions testing
- Immunity testing
- Laboratory accreditation verification
PSE Mark (Japan)
PSE (Product Safety Electrical Appliance & Material) mark indicates compliance with Japanese electrical safety standards. Mini turbo jet fans require PSE certification for legal sale in Japan.
The mark applies to electrical appliances under the Electrical Appliance and Material Safety Law. Testing covers electrical safety, construction requirements, and performance standards.
PSE mark for small blowers requires factory inspections and ongoing compliance monitoring. Manufacturers must register with Japanese authorities and maintain quality systems.
Certification Process:
- Laboratory testing by designated bodies
- Factory inspection requirements
- Annual surveillance audits
- Registration with METI (Ministry of Economy, Trade and Industry)
UKCA Mark (United Kingdom)
UKCA (UK Conformity Assessed) mark replaced CE marking for the UK market after Brexit. Mini turbo jet fans require UKCA electric fan approval for sale in Great Britain.
The marking covers electrical safety, electromagnetic compatibility, and product-specific requirements. Standards align closely with previous EU requirements but follow UK-specific procedures.
Manufacturers must use UK-based conformity assessment bodies for certain procedures. The UKCA mark must be clearly visible on products or packaging.
Key Features:
- Electrical safety compliance
- EMC requirements
- UK-based testing and certification
- Post-Brexit market access requirement
California Proposition 65 (CACA65)
California Proposition 65 requires warnings for products containing chemicals known to cause cancer or reproductive harm. Mini turbo jet fans may require CACA65 chemical warning labels.
The law applies to products sold in California containing listed chemicals above safe harbor levels. Manufacturers must evaluate chemical content and provide appropriate warnings.
Warning labels must follow specific format requirements and placement guidelines. Non-compliance results in enforcement actions and potential penalties.
Warning Requirements:
- Chemical exposure assessment
- Standardized warning language
- Prominent label placement
- Website warning notifications for online sales
UL And ETL Listings (North America)
UL (Underwriters Laboratories) and ETL (Intertek Testing Services) provide safety testing and certification for electrical products. UL ETL listed portable fan certification demonstrates compliance with North American safety standards.
Both organizations test products to identical safety standards but operate as competing certification bodies. Manufacturers may choose either UL or ETL for product certification.
Testing covers electrical safety, fire hazard assessment, and mechanical safety requirements. Listed products receive certification marks and database listings.
Certification Benefits:
- Market acceptance and credibility
- Insurance and liability considerations
- Retailer requirement compliance
- Consumer safety assurance
Testing And Approval Processes
Mini turbo jet fans undergo rigorous laboratory testing for electrical safety parameters including voltage endurance and insulation resistance measurements. Factory production control systems ensure consistent quality through regular sample audits and documentation reviews.
Laboratory Type Tests (Voltage Endurance, Insulation Resistance)
Laboratory testing begins with dielectric strength tests that verify the fan’s ability to withstand electrical stress. These tests apply high voltage between conductive parts and the housing to ensure proper insulation integrity.
Insulation resistance measurement forms a critical component of electrical safety evaluation. Test laboratories measure resistance between live parts and accessible conductive surfaces using standardized procedures.
High-voltage endurance testing subjects fans to sustained electrical stress over extended periods. The equipment must maintain safe operation without breakdown or degradation of insulation materials.
Electromagnetic compatibility testing evaluates interference potential and susceptibility to external electromagnetic fields. This ensures the fan operates safely in various electrical environments without causing disruption.
Performance testing validates airflow rates, power consumption, and thermal characteristics against manufacturer specifications. These measurements confirm the fan meets stated operational parameters under controlled conditions.
Factory Production Control And Sample Audits
Manufacturers implement factory production control systems to maintain consistent quality standards throughout production cycles. These systems include documented procedures for materials inspection, assembly verification, and final testing protocols.
Regular sample audits involve random selection of finished products for comprehensive testing. Independent inspectors verify compliance with approved specifications and safety requirements through systematic evaluation.
Regulatory documentation and marking requirements mandate proper labeling and certification marks on each unit. Manufacturers must maintain traceability records linking individual products to specific test results and quality control data.
Production facilities undergo periodic assessments to verify continued compliance with approved manufacturing processes. These audits ensure ongoing adherence to safety standards and quality management systems.
Role Of Accredited Test Houses
TÜV Rheinland and SGS represent leading accredited test houses that provide independent safety certification services. These organizations maintain specialized laboratories equipped for comprehensive mini turbo jet fan evaluation.
Accredited facilities conduct risk assessment and hazard analysis to identify potential safety concerns. They evaluate mechanical, electrical, and thermal hazards through systematic testing protocols.
Testing laboratories must demonstrate competence through regular accreditation renewals and proficiency testing programs. This ensures reliable and consistent evaluation of safety compliance across different manufacturers.
Test houses provide certification marks and documentation that enable market access in various jurisdictions. Their independent verification gives consumers and regulators confidence in product safety and performance claims.
Manufacturer Quality Systems
Mini turbo jet fan manufacturers implement ISO 9001:2015 frameworks for systematic production oversight. Factory testing protocols include mechanical vibration assessments and 8-hour electrical endurance validation to ensure component reliability.
ISO 9001:2015 Certification For Process Control
ISO 9001:2015 certification establishes documented quality management systems within electronics factories. The standard requires manufacturers to maintain consistent production processes through documented procedures and regular audits.
Supply-chain quality management forms a core component of ISO 9001 compliance. Manufacturers must verify supplier capabilities and monitor incoming component quality through inspection protocols.
Factory production control systems track each manufacturing stage from raw materials to finished products. Documentation requirements include process parameters, inspection results, and corrective action records.
Quality assurance teams conduct internal audits to verify adherence to established procedures. These audits identify process deviations and implement corrective measures before products reach customers.
In-House Test Machines (Life-Cycle, Vibration, Insertion/Extraction)
Manufacturers utilize specialized equipment to validate mini turbo jet fan durability under operational conditions. Life-cycle testing machines simulate thousands of start-stop cycles to identify potential failure modes.
Mechanical vibration life-cycle tests subject fans to controlled oscillations at various frequencies. These tests replicate real-world vibration exposure during equipment operation and transportation.
Insertion and extraction testing verifies connector durability through repeated mating cycles. Automated test fixtures perform hundreds of connection cycles while monitoring electrical continuity and mechanical wear.
Test Type | Duration | Parameters Monitored |
---|---|---|
Life-cycle | 10,000-50,000 cycles | Motor performance, bearing wear |
Vibration | 24-72 hours | Structural integrity, noise levels |
Insertion/Extraction | 500-1,000 cycles | Connector resistance, mechanical fit |
8-Hour High-Voltage Endurance And Insulation Checks
High-voltage endurance testing applies elevated voltages to fan components for extended periods. The 8-hour test duration exceeds typical operational stress levels to identify insulation weaknesses.
Insulation resistance measurements verify electrical safety between conductors and ground connections. Test voltages typically range from 500V to 1,500V depending on fan specifications.
Temperature monitoring during endurance testing ensures components remain within safe operating limits. Excessive heat generation indicates potential insulation breakdown or component degradation.
Pass/fail criteria specify minimum insulation resistance values and maximum leakage current thresholds. Components failing these tests require design modifications or material upgrades before production approval.
Verifying A Certification Mark
Proper verification involves examining official documentation from testing laboratories and confirming authentic certification labels match registered designs. Manufacturers should provide batch-specific test reports that demonstrate compliance with current safety standards.
Checking Official Certificates And Reports
Genuine certification documents contain specific identifiers that distinguish them from counterfeit versions. Each certificate includes the testing laboratory’s accreditation number, digital signatures, and unique document reference codes.
Safety auditors verify these elements against official databases maintained by certification bodies. The certificate must list the exact model number, testing standards used, and validity dates for the certification period.
Testing reports should detail the specific safety parameters measured during evaluation. These include electrical safety ratings, thermal protection limits, and electromagnetic compatibility results for mini turbo jet fans.
Original certificates display watermarks, security features, and contact information for the issuing laboratory. Manufacturers cannot modify these documents without invalidating the certification status.
Spotting Genuine Labels On Product And Packaging
Authentic certification marks feature precise typography, correct color schemes, and registered trademark symbols. Counterfeit labels often show blurred text, incorrect fonts, or missing security elements that distinguish genuine marks.
Each certification body maintains detailed specifications for label appearance and placement requirements. The mark’s size, position, and accompanying text must match official guidelines provided by the certifying organization.
Holographic elements, raised printing, or special inks protect genuine labels from reproduction attempts. These security features become visible under specific lighting conditions or when viewed from different angles.
The certification number printed on labels must correspond with database entries maintained by the issuing authority. Safety auditors cross-reference these numbers during compliance inspections to verify authenticity.
Requesting Batch-Specific Test Documentation
Manufacturers maintain test records for each production batch that demonstrate ongoing compliance with safety standards. These documents prove that certified designs undergo consistent quality control throughout manufacturing processes.
Batch documentation includes material composition reports, electrical safety test results, and thermal performance measurements. Each report contains timestamps, inspector signatures, and traceability information linking products to specific manufacturing dates.
Testing frequency varies by certification requirements, but most standards mandate regular verification testing. Manufacturers must provide evidence that safety parameters remain within acceptable limits for each production run.
Safety auditors review batch records during facility inspections to confirm compliance with certification requirements. Missing or incomplete documentation may indicate non-compliance with approved safety standards.
Introducing Kinzir And Its Mini Turbo Jet Fans
Kinzir operates as a specialized manufacturer focusing on compact turbine technology with established quality control systems and multiple industry certifications. The company produces mini turbo jet fans designed for various applications while maintaining strict engineering standards.
Company Profile
Kinzir specializes in developing and manufacturing mini turbo jet fans for commercial and industrial applications. The company was established in 2018 and operates from facilities in Germany.
The manufacturer focuses on compact turbine technology. Their engineering team consists of 15 specialists with backgrounds in aerospace and mechanical engineering.
Kinzir serves customers across Europe, North America, and Asia. The company maintains partnerships with distributors in 12 countries.
Their product development cycle typically spans 18 months from concept to market release. The company invests approximately 20% of annual revenue into research and development activities.
Production And Quality Control
Kinzir operates a 25,000 square foot manufacturing facility equipped with CNC machining centers and automated assembly lines. The facility processes aluminum and titanium components for fan assemblies.
Quality control procedures include dimensional inspection at three production stages. Each mini turbo jet fan undergoes performance testing before packaging.
The company maintains ISO 9001:2015 certification for quality management systems. Production capacity reaches 500 units per month across all product lines.
Materials undergo incoming inspection using coordinate measuring machines. Final assembly occurs in controlled environment chambers to prevent contamination.
Testing protocols include vibration analysis, thermal cycling, and endurance runs. Each unit receives individual performance certification documenting thrust output and operational parameters.
Certifications Held
Kinzir holds CE marking for European market compliance. The company maintains ISO 14001 environmental management certification.
Their mini turbo jet fans carry UL listing for electrical safety standards. Products meet FCC Part 15 electromagnetic compatibility requirements.
The manufacturer obtained AS9100D aerospace quality certification in 2023. This certification covers design, production, and testing procedures.
REACH compliance documentation exists for all materials used in fan construction. The company maintains RoHS certification for electronic components.
Annual audits verify continued compliance with all held certifications. Third-party testing laboratories validate performance claims and safety standards.
Mini Turbo Jet Fan Highlights
Kinzir produces three primary models: the K-200, K-350, and K-500 series. These fans generate thrust outputs ranging from 2.5 to 12 pounds.
The K-200 measures 4.2 inches in diameter and weighs 1.8 pounds. It operates at maximum speeds of 85,000 RPM with electronic speed control.
Fan design incorporates titanium compressor blades and aluminum housing construction. Each model features integrated temperature monitoring and automatic shutdown protection.
The K-500 series includes variable pitch inlet guide vanes for improved efficiency. All models operate on standard 12V or 24V DC power systems.
Noise levels range from 68 to 78 decibels at maximum thrust settings. The fans include mounting hardware and control electronics as standard equipment.
Best Practices For Buyers And Suppliers
Buyers should specify exact certification requirements in purchase orders and maintain detailed compliance records. Suppliers must demonstrate ongoing adherence to safety standards through factory audits and proper documentation for customs clearance.
Specifying Required Marks In Purchase Orders
Purchase orders must clearly state required certification marks such as CE, UL, FCC, and RoHS compliance. This prevents confusion and ensures suppliers understand exact requirements before production begins.
Buyers should include specific standard numbers like IEC 60335-2-80 for motor-operated appliances or ISO 9001 for quality management systems. Each certification requirement should list the applicable market regions.
The purchase order must specify that products without proper markings will be rejected at inspection. This clause protects buyers from receiving non-compliant products that cannot clear customs.
Documentation requirements should include certificates of conformity, test reports, and declaration of conformity documents. Suppliers must provide these materials before shipment to avoid delays at borders.
Including Compliance Checks In Factory Audits
Factory audits must verify that production facilities maintain valid ISO certifications and follow documented quality control procedures. Auditors should examine testing equipment calibration records and maintenance logs.
Production line inspections should confirm that safety testing occurs at specified intervals during manufacturing. Workers must demonstrate proper procedures for electrical safety testing and performance verification.
Maintenance and inspection protocols require documentation showing regular equipment servicing and safety system checks. Audit teams should review these records to ensure consistent compliance with safety standards.
Quality control documentation must show batch testing results and rejection rates for non-conforming products. This data demonstrates the supplier’s commitment to maintaining certification standards throughout production.
Keeping Certificates On Record For Customs Clearance
Customs and import compliance requires maintaining current certificates of conformity for each product model and destination country. These documents must be readily accessible during import procedures.
Electronic filing systems should organize certificates by product model, certification body, and expiration dates. This system enables quick retrieval when customs officials request documentation.
Expired certificates can result in shipment delays or rejection at border crossings. Companies must track renewal dates and obtain updated documentation before current certificates expire.
Import brokers need access to complete certification packages including test reports, factory inspection certificates, and compliance declarations. Missing documentation can trigger costly customs examinations and storage fees.
Conclusion
Certified mini turbo jet fans provide measurable safety benefits and operational reliability through standardized testing protocols. Procurement decisions should prioritize suppliers who offer comprehensive documentation and sample testing opportunities.
Recap Of Why Certified Mini Turbo Jet Fans Deliver Value
Certified mini turbo jet fans undergo rigorous testing for electrical safety, thermal performance, and mechanical integrity. These certifications reduce workplace hazards by ensuring products meet established safety thresholds.
UL, CE, and FCC certifications validate that fans operate within safe temperature ranges and electrical specifications. This testing eliminates guesswork about product reliability in industrial applications.
User safety benefits include reduced fire risk, electromagnetic interference protection, and consistent performance under load. Operational guidelines become more straightforward when manufacturers provide certified specifications and installation requirements.
Quality control processes for certified products typically include batch testing and traceability documentation. These measures ensure consistency across production runs and enable faster troubleshooting when issues arise.
Next Steps: Request Samples And Test Reports From Your Supplier
Contact potential suppliers to request physical samples of certified mini turbo jet fans for evaluation. Request copies of current certification documents including UL listings, CE declarations, and FCC test reports.
Verify that test reports match the specific model numbers being considered for purchase. Check certification dates to ensure documents remain valid and current with latest safety standards.
Schedule performance testing of samples under actual operating conditions. Document temperature readings, noise levels, and airflow measurements against manufacturer specifications.
Request operational guidelines documentation including installation procedures, maintenance schedules, and safety precautions. Evaluate whether supplier technical support can assist with integration and troubleshooting requirements.
Frequently Asked Questions
Mini turbo jet fans require specific safety certifications and testing procedures to meet regulatory standards across different markets. Understanding these requirements helps manufacturers and users ensure proper compliance with international safety protocols.
What are the common safety certifications required for mini turbo jet fans?
Mini turbo jet fans typically require UL certification for North American markets and CE marking for European Union distribution. These certifications verify electrical safety, electromagnetic compatibility, and mechanical integrity standards.
FCC certification addresses electromagnetic interference requirements in the United States. CSA certification serves as an alternative to UL for Canadian markets.
Industry associations like the Air Movement and Control Association provide additional guidelines for performance standards. Some applications may require ATEX certification for explosive atmosphere compliance.
How do mini turbo jet fans adhere to international safety standards?
International Electrotechnical Commission (IEC) standards form the foundation for global safety requirements. IEC 60335 covers household electrical appliances, while IEC 60034 addresses rotating electrical machines.
ISO 9001 quality management standards ensure consistent manufacturing processes. RoHS compliance restricts hazardous substances in electronic components.
Manufacturers must demonstrate compliance with noise emission standards under ISO 3744. EMC Directive 2014/30/EU governs electromagnetic compatibility requirements in Europe.
What testing processes do mini turbo jet fans undergo before certification?
Electrical safety testing includes insulation resistance, leakage current, and dielectric strength measurements. Temperature rise testing verifies thermal performance under maximum load conditions.
Vibration testing evaluates mechanical durability over extended operating periods. Electromagnetic compatibility testing measures conducted and radiated emissions.
Third-party testing laboratories conduct independent verification of performance claims. Regulatory bodies require documented test reports before issuing certifications.
Can mini turbo jet fans be used in hazardous environments, and what standards cover their safety?
ATEX Directive 2014/34/EU governs equipment for explosive atmospheres in Europe. NEC Class I, II, and III classifications define hazardous location requirements in North America.
Intrinsically safe designs prevent ignition of flammable gases or dust particles. Ex markings indicate specific protection methods and environmental limitations.
IP rating standards determine ingress protection against moisture and particulates. Most hazardous location applications require IP65 or higher ratings.
What is the significance of UL and CE markings on mini turbo jet fans?
UL markings indicate compliance with Underwriters Laboratories safety standards for electrical products. These markings verify fire safety, electrical shock protection, and mechanical hazard prevention.
CE markings demonstrate conformity with European Union safety directives. Manufacturers self-declare compliance based on technical documentation and testing results.
These markings enable legal distribution in respective markets. Insurance companies often require certified products for coverage eligibility.
How often should mini turbo jet fans be inspected or recertified to ensure continued safety compliance?
Annual inspections verify continued compliance with safety standards in commercial applications. Industrial environments may require quarterly or monthly inspection schedules.
Regulatory bodies typically require recertification every three to five years for significant design changes. Manufacturing process modifications may trigger immediate recertification requirements.
Industry associations recommend documenting inspection procedures and maintaining service records. Preventive maintenance schedules help identify potential safety issues before certification expiration.